When you go to high school, probably the last thing you expect to do is create a part that will be used by NASA, but that’s exactly what Medway resident and recent graduate Dominic Parrella was able to do as an engineering shop major at Tri-County Regional Vocational Technical High School in Franklin. The school is part of NASA’s HUNCH program (High School Students Unite with NASA to Create Hardware), and advanced manufacturing is part of the engineering shop. The school even has an advanced manufacturing facility.
“HUNCH prototype and design is where NASA has a list of problems, and they put it out to all the schools that do HUNCH,” explains Parrella. “NASA would send us a blueprint, and we had to create that project with all the tolerances and features they want. They sent us the metal they wanted it to be in. Our dimension could only be 1/5000th of an inch below the target dimension.”
Dominic came in on the project after another student had begun it, working with teacher Jeffrey McCall.
“A different student sautered the project early in the year, but he went out on coop,” says McCall. “Dom picked it up right after we went through the design phase very early on in the project.”
“We had to actually make the part,” says Dominic, of the ISS flight hardware parts, called actuators. “Mr. McCall went through the designing the tool paths, and so I had to do all the set-up work on the machine, setting up the softjaws and getting tool offsets and work offsets. After we actually milled out the pieces, I had to do the deburring on the edges to make sure they’re not sharp—the quality control (QC) work, and (make sure) all the dimensions were the right dimensions. It doesn’t matter if it looks good as much as if it’s right. It’s definitely more important to get the right dimensions. If you have it wrong, it’s just not going to work.”
“This is actually (Tri-County’s) 1st year that we had been manufacturing hardware for (NASA),” says Jeffrey McCall, who began three years ago at the school, taking over where teacher Kristin Maggis had left off with the HUNCH program. “We had been working on the prototype, such as the things astronauts can use in space, like storage and bedding, things of that nature. It wasn’t until this year that we really had the capacity to do something like that.”
“Probably the most impressive part of this was that we milled 11 parts out, and those were our first 11 parts,” says Dominic. “All 11 of them were perfect, and they loved the parts. They had great surface finishes, no burrs, no sharp edges. The actuators had to fit into other small pieces.”
Dominic realizes he had a unique opportunity in working on this project.
“The project was almost a simulation, a real job you’d have in a real manufacturing facility. We had a lot of unique teaching moments, and it was a really fun experience,” says Dominic, who benefitted by being the sole student working on the project with Mr. McCall. “There are certain lessons I don’t think Mr. McCall would have been able to teach.” Parrella, who’ll be headed to UMass Dartmouth for mechanical engineering in the fall, is grateful, he says, for the time Mr. McCall took to teach him. “He could very well have just instantly fixed the project without me knowing, but he took the time and purposefully taught me every time. The project overall was just an amazing learning experience.”
“So, a lot of these projects that we’re doing, this project in particular, you don’t always know the end result of what you’re making is. You may not have that mating part. We made an actuator, and it actually goes to some other part that another school is making. It’s important that they fit together, and that is a real-world scenario, on top of doing something for NASA, which is a highly recognizable organization. It’s quite an opportunity for a young kid to be able to do something like that.”
also getting a tight job (
There’s one more perk to working with the NASA HUNCH program, says Dom.
“My name’s going to be up in space twice,” he says.
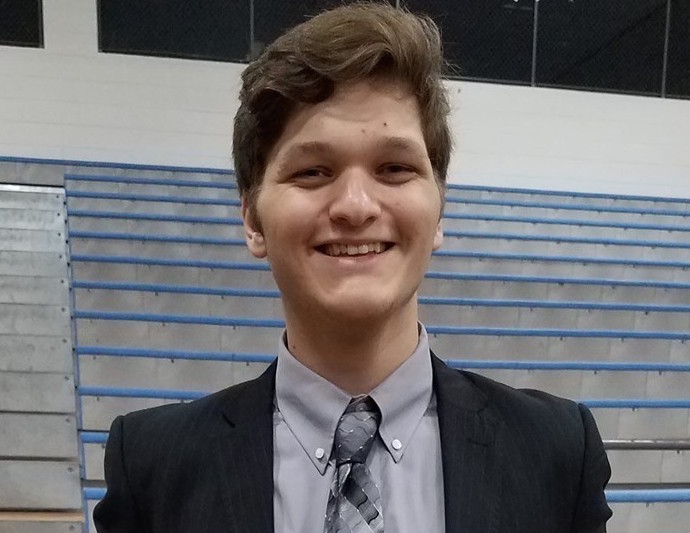
Issue Date:
August, 2019
Article Body: