Franklin residents might have heard something about the old machines at the former Clark, Cutler & McDermott being fired up to manufacture personal protective equipment (PPE). For the past month, a lot of work has been going on behind the scenes to make this happen.
Entrepreneur Peter Berzin, who is involved in a number of different ventures from IT consulting to Real Estate investment, explains how the idea began.
“Beginning in April, we were discussing with a friend of mine, Isaac Carter, and Norb Jankowski how we can help during this time of the pandemic.” During the course of the conversation, Norb realized cutter machines were in the Franklin facility.
Norb Jankowski, a Michigan resident, was once a liaison bet General Motors and Clark, Cutler, McDermott.
“Basically, it just dawned on me that this equipment was up here,” says Jankowski, who had last visited the site about three years ago, after GM had taken over the building. “I did some reachout, and if it wasn’t for Tom (Mercer) and Jeff Roy, we would be spinning our wheels.”
“This all started with a telephone call on March 30,” says Roy. “Tom Mercer, Chair of the Franklin Town Council, had heard from a former engineer with Clark, Cutler, McDermott. CCM was the manufacturer of sound-deadening equipment for automobiles and was a supplier to GM. That company went into financial difficulty, with the factory vacant. The new owner has some grand plans for it.”
“We’re happy to let them use the equipment in the property and to use the property,” says Rick Kaplan, who owns the property with partner Casey Killam. “My partner and I are not machinists, but we’re told that they can take the big presses and make medical gowns, isolation gowns. If they are able to make these, we are happy to let them use the equipment and facility.”
“There are a few more hurdles they have to overcome, but a lot of things have happened,” says Mercer. “These are the kinds of little nuances, the i’s to get dotted, the t’s need to get crossed.”
Mercer and Roy have worked to help the potential manufacturers connect with state and federal funding as well as building code issues and other legal processes.
“The Commonwealth of Massachusetts has set up a manufacturing task force (MassMEP) to address the need for PPE,” says Roy. “All ideas are centralized and get processed by this website. Every state has one of these, and then I put them in touch with some federal funding they could apply for—the deadline was 24 hours later. There’s a desperate need for (PPE), and I’d love to see it happen in Franklin,” says Roy.
“Seeing that they have created an entire network, Mass MEP (masstech.org), Mass ERT (https://masstech.org/manufacturing-emergency-response-team-funding-program), all of these people on board to help do something and bring a solution to the state, that just ignited me from there,” say Berzin. “The only way this will work is if you have the support from that type of level.”
Berzin and his colleagues created Contollo Mass Manufacturing, LLC, with a business and process plan and reached out to other business owners. Mass MEP Mercer connected them to The Cooley Group, of Pawtucket, RI, which manufactures a material used in billboards,
“We designed a pattern where we would stamp it out and only have two seams by putting two sleeves together,” says Berzin. That process reduced the time needed to make an isolation gown to just 30 seconds, down from 5-8 minutes. The David Scott Company, also in Franklin, will handle distribution, as well as, initially, the welding of the material, something Berzin expects will be later brought in-house.
Vartest Company, of New York, tested the material, which passed at levels 1, 2, 3 and 4 in terms of being compliant for surgical gowns. “That’s the highest level you can go,” says Berzin. “It’s basically the strongest gown you can use, and it’s reusable, environmentally-friendly material. So, we had to create prototypes and samples, and send them in for compliance testing, for seams and durability, to wash it and make sure it will last multiple uses. At press time, laundering remained the final test of the prototype, which had been modified with feedback from surgeons from Milford Regional Medical Center.
“The doctors at Milford loved it,” says Mercer. “The disaster team over there thought it was really good. They offered a couple of suggestions to be made by the team putting this together.” He adds that all of the materials and gowns will be made in the USA.
Berzin has been contacted by people from Massachusetts to California looking for gowns.
“We’re just waiting to start production,” he said, in the last week of April. “It should take about two to three weeks to ramp up to 100,000 gowns every 10 days. Our calculated hope is by May 4th.”
With the prototype having passed a number of approvals, Berzin was confident the gowns were on their way to being produced. “We’re working with a gentleman at MIT who’s helping us with the final testing,” says Berzin.
By press time, the cutters were already revived. “Ninety percent of it is mechanical and already running,” says Berzin, who was working with building inspectors and fire marshals to ready the space.
He envisions an operation using technology to achieve full automation and hopes, down the road, to expand beyond isolation gowns to possibly face shields and, perhaps, “smart” N95 masks.
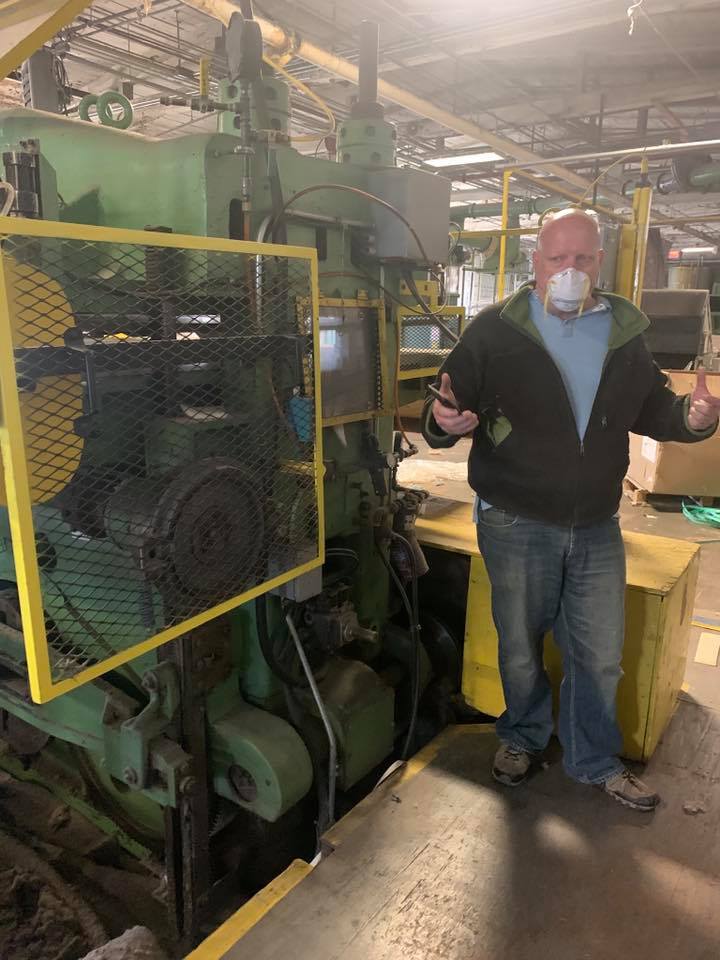
Issue Date:
May, 2020
Article Body: